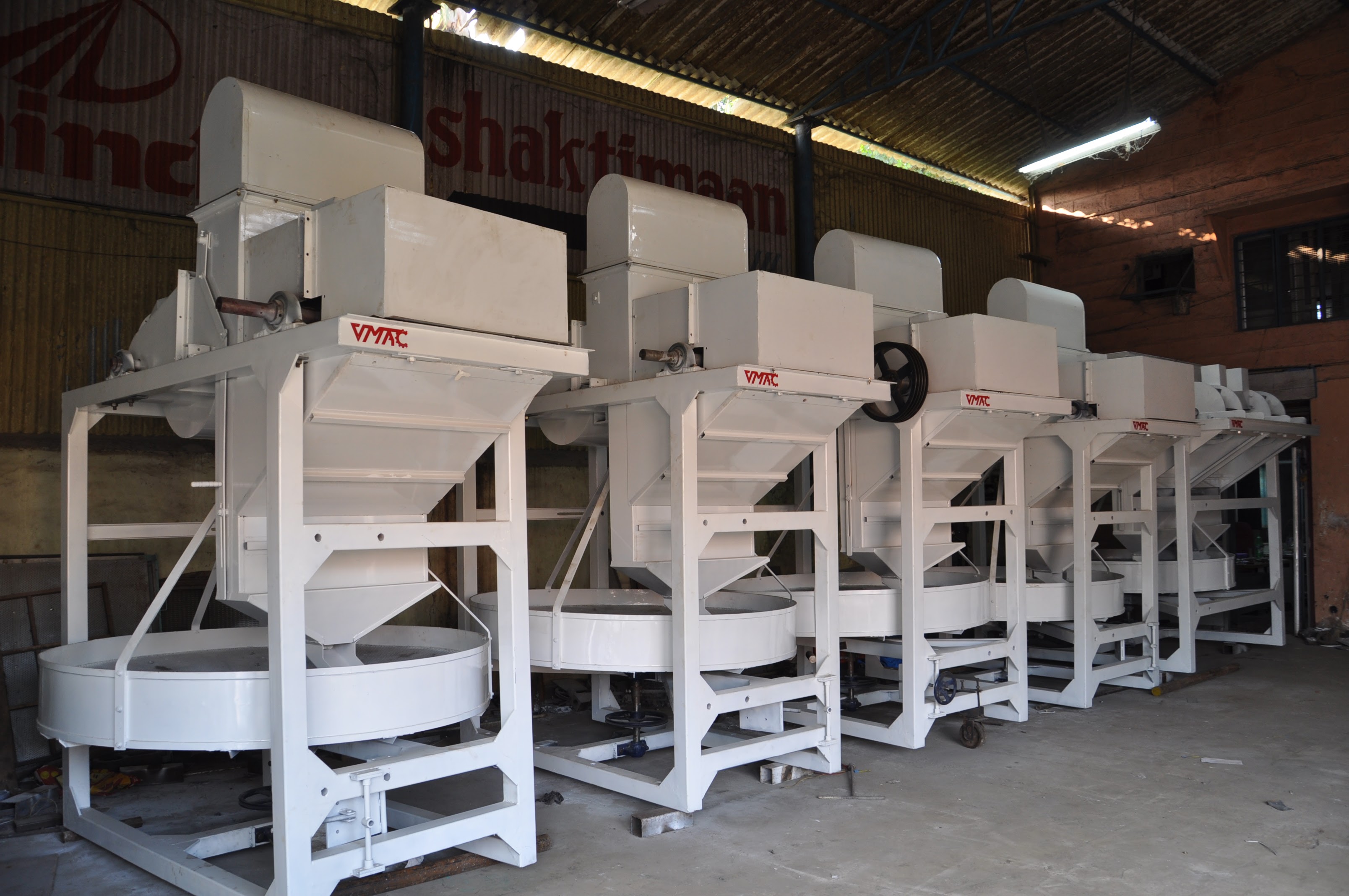
Production
Mastering Coffee Production
At Vmac Industries, we've mastered the balance between traditional craftsmanship and modern technology.
Extend the lifespan of your coffee processing equipment with expert maintenance tips from industry professionals, ensuring optimal performance and minimizing downtime.
Proper maintenance of your coffee processing equipment is essential for sustaining efficiency, ensuring product quality, and protecting your investment. Regular upkeep not only prevents unexpected breakdowns but also enhances the longevity of your machinery. In this comprehensive guide, industry specialists share valuable maintenance advice to keep your operations running smoothly.
Regular maintenance is vital for several reasons:
Optimized Performance: Ensures equipment operates at peak efficiency.
Extended Lifespan: Reduces wear and tear, prolonging the machinery's life.
Cost Savings: Prevents costly repairs and production losses due to downtime.
Safety: Minimizes the risk of accidents caused by equipment failure.
Neglecting maintenance can lead to decreased productivity, inferior product quality, and unexpected expenses.
An effective maintenance schedule includes:
Routine Inspections: Regular checks to identify potential issues early.
Preventive Maintenance: Scheduled servicing to prevent breakdowns.
Record Keeping: Documenting maintenance activities for reference.
Inventory Your Equipment: List all machinery and their specifications.
Consult Manufacturer Guidelines: Follow recommended maintenance intervals.
Assign Responsibilities: Designate team members for specific tasks.
Set Reminders: Use calendars or software to track maintenance dates.
Our Maintenance Services can assist in creating a customized maintenance plan.
Implementing daily routines helps maintain equipment health:
Cleaning: Remove dust, debris, and residue from all machinery surfaces.
Visual Inspections: Check for signs of wear, leaks, or damage.
Lubrication: Apply lubricants to moving parts as needed.
Operational Checks: Ensure controls and safety features are functioning properly.
Use appropriate cleaning agents to avoid damaging equipment.
Document any irregularities and report them immediately.
Perform more in-depth inspections periodically:
Alignment and Calibration: Ensure machines are correctly aligned and calibrated for optimal performance.
Component Inspection: Examine belts, chains, bearings, and other components for wear.
Electrical Systems: Check wiring, connectors, and sensors for signs of deterioration.
Software Updates: Update firmware or software in automated systems.
Regular checks help catch issues that may not be evident during daily routines.
Annual maintenance often involves:
Comprehensive Overhaul: Disassemble critical components for thorough inspection.
Replacement of Worn Parts: Proactively replace parts nearing the end of their lifespan.
System Upgrades: Implement technological enhancements or retrofits.
Safety Audits: Review safety protocols and equipment compliance.
Scheduling annual maintenance during off-peak seasons minimizes production disruptions.
A well-trained team is essential for effective maintenance:
Operational Training: Ensure staff understand how to operate equipment correctly.
Maintenance Procedures: Teach proper cleaning and basic servicing techniques.
Safety Protocols: Emphasize the importance of safety during maintenance tasks.
Consider our Comprehensive Equipment Training programs to enhance your team's skills.
Professional maintenance services offer:
Expertise: Technicians with specialized knowledge of your equipment.
Efficiency: Faster diagnosis and repair of issues.
Access to Genuine Parts: Ensures compatibility and quality.
Warranty Protection: Maintains compliance with manufacturer warranties.
Engaging professionals can be cost-effective by preventing major breakdowns and extending equipment life.
Different machines require tailored maintenance approaches.
Inspect Hulling Surfaces: Check for wear or damage to hulling discs or drums.
Adjust Clearance Settings: Ensure proper spacing to prevent bean damage.
Clean Chutes and Screens: Remove husk buildup to maintain efficiency.
Visit our Coffee Huller page for more details.
Check Pulping Plates: Look for signs of wear that could affect performance.
Monitor Water Usage: Ensure water jets are functioning and not clogged.
Lubricate Moving Parts: Maintain smooth operation and reduce friction.
Learn more about pulper maintenance at Coffee Pulper.
Balance Adjustment: Verify that the deck is correctly balanced for accurate separation.
Screen Cleaning: Keep screens free from debris to prevent clogging.
Fan Maintenance: Ensure fans are clean and functioning properly.
For specifics, see our Gravity Separator information.
Addressing common issues proactively:
Equipment Wear: Regularly replace consumable parts before failure.
Unexpected Downtime: Keep spare parts on hand to reduce repair time.
Skill Gaps: Provide ongoing training to keep staff up-to-date.
Budget Constraints: Prioritize maintenance in budgeting to avoid costly emergencies.
Effective planning and resource allocation help mitigate these challenges.
Proper maintenance is a critical component of successful coffee processing operations. By implementing regular maintenance schedules, training your team, and utilizing professional services, you can ensure that your equipment performs optimally. This proactive approach not only safeguards your investment but also enhances product quality and operational efficiency.
Develop a Maintenance Plan: Start by creating a comprehensive schedule.
Train Your Team: Invest in training programs for your staff.
Consult Professionals: Reach out to our experts via Contact Us for specialized assistance.
Explore Maintenance Services: Visit our Maintenance Services page to learn how we can support your maintenance needs.
For more expert insights, visit our Blogs section.
Lastest blog posts